Skip to content
Sign and Tag Requirements
In all workplaces, it is critical to have signs, tags, and labels to point out potential hazards. OSHA has clear guidelines on how to use signs and tags to help prevent accidents for workers, the public, or both. Signs and tags are also important to avoid property damage. OSHA’s guidelines are meant to cover all safety signs except those designed for streets, highways, railroads, plant bulletin boards, and safety posters.
Signs 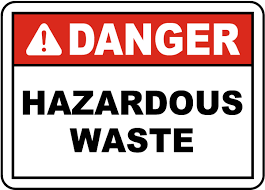
According to OSHA, a “sign” is a surface on which there is the warning or safety instructions for industrial workers or members of the public who may be exposed to hazards. This definition does not include news releases, safety posters, or bulletins used for employee education. There are many kinds of signs, including danger signs, caution signs, and safety instruction signs.
For danger signs, there cannot be any variation in the type of design of signs posted to warn of specific dangers and radiation hazards, according to OSHA. All employees should be trained to understand that danger signs indicate immediate danger and that special precautions are necessary. Caution signs should only be used to warn against potential hazards or to warn against unsafe practices. Employers should make sure their workers know that caution signs indicate a possible hazard and that they need to take proper precautions. Safety instruction signs must be used where there is a need for general instructions and suggestions relative to safety measures.
OSHA also has specific requirements for how signs are designed. All signs must have rounded or blunt corners, without any sharp edges, burrs, splinters, or other sharp projections that could cause a hazard. The ends or heads of the bolts used attach signs or other fastening devices must be situated in a way that does not cause a hazard to anyone. Danger signs must be red, black, and white. Caution signs must have a yellow background with black letters, or a black background with yellow letters. Safety instruction signs should have a white background with black letters, or green with white letters. All kinds of signs need to be glossy and opaque.
Signs must be worded clearly and concisely and should contain sufficient information that can be easily understood by those who will be reading them. The wording should also make a positive suggestion as opposed to a negative one, and the information should be accurate and factual.
OSHA provides specific guidelines for biological hazard signs, which should be used to signify the actual or potential presence of a biohazard. These signs can also be used to point out equipment, containers, rooms, materials, experimental animals, or combinations of these, which contain or are contaminated with viable hazardous agents. In this case, OSHA defines “biological hazard” or “biohazard” as infectious agents presenting a risk or potential risk to the well-being of people. 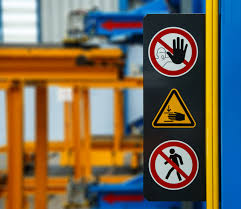
Tags
Accident prevention tags are used to identify hazardous conditions and provide a message to employees that meets OSHA’s standards and requirements. OSHA defines a “tag” as a device usually made of card, paper, pasteboard, plastic, or other material whose purpose is to identify a hazardous condition. Employers should use tags to prevent accidental illness or injury to employees who are exposed to hazardous or potentially hazardous conditions, equipment, or operations that are out of the ordinary, unexpected, or not immediately apparent. Tags should remain present until the hazard has been eliminated or the hazardous operation is completed. Employers should also take note that tags do not need to be used where signs, guarding, or other positive means of protection are being used.
All tags must contain a signal word and a major message. The signal word is the portion of the tag’s inscription that contains the word or words that are intended to capture the worker’s immediate attention. The major message is more specific than the signal word, indicating the specific hazardous condition or the instruction that the employee needs to know. Examples of signal words include “Danger,” “Caution,” or “BIOHAZARD,” and examples of major messages include “High Voltage,” “Close Clearance,” “Do Not Start,” or “Do Not Use.”
The signal word on a tag must be readable at a minimum distance of 5 feet, or a greater distance depending on the specific hazard. The major message on a tag can be presented in either written text or pictographs, or both. Tags should be affixed as close and as safely as possible to the hazard they indicate by a positive means such as string, wire, or adhesive that prevents them from falling off, getting lost, or unintentionally removed. Both the signal word and major message should be understandable to all employees who are at risk of exposure, and all workers must be trained to recognize the meanings of the different tags used throughout their workplace and what precautions to take when necessary.
There are four main types of tags:
-
Danger tags: use in major hazard situations where an immediate hazard presents a threat of death or severe injury.
-
Caution tags: use in minor hazard situations where a non-immediate or potential hazard or unsafe practice presents a lesser threat of injury.
-
Warning tags: use to represent a hazard level between caution and danger, instead of the required caution tag, as long as they have a signal word of warning, an appropriate message, and meet the general tag criteria.
-
Biological hazard tags: use to identify the actual or potential presence of a biological hazard and to identify equipment, containers, rooms, experimental animals, or combinations of these that contain or are contaminated with biological agents.
Other tags may be used in addition to the required tags, or in situations where they are not required, as long as they do not take away or distract from the signal word and major message of the required tags.
For more information or assistance with your Environmental and Health & Safety regulatory compliance needs, contact Ralph Carito at Total Environmental & Safety, LLC (Total) at rcarito@TotalEnviron.com or 908-442-8599.
Thank you for your continued support. If you like what you read in Total’s Monthly EHS Newsletter, please tell your friends and colleagues.
We always appreciate hearing from you, so if you have a suggestion, comment or gripe, please drop us a line at: contact@TotalEnviron.com or call us at 908-442-8599.
Total Environmental & Safety’s (Total’s) most recent blog. Let us know if you enjoyed it.
Page load link