Skip to content
Proper PPE and Worker Safety Go Hand-in-Hand
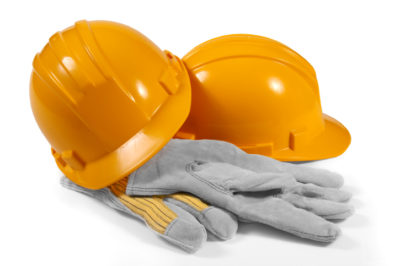
Hand injuries are among the most common workplace injuries, and they are also some of the most preventable.
According to the most recent data available from the Bureau of Labor Statistics, there were over 121,800 hours lost on the jobsite in 2017 due to hand injuries. For those who seek medical treatment for these types of injuries, it can cost an average of $22,384. Within these cases, 70% of the hand injuries occurred when users were not even wearing gloves to protect themselves while working.
Despite the severity of these injuries and the overwhelming statistics that highlight the necessity of hand protection, there is still a lot of confusion surrounding what needs to be considered when choosing a worker’s hand protection. It is critical to understand that not all hand protection is created equal. Proper hand protection is critical, however, as standards evolve, and workers often question which solution to use. In turn, this frustration often deters users from taking advantage of any sort of hand protection at all.
Understanding the differences between each type of hand protection is difficult—even for safety professionals. There are multiple factors and jobsite requirements that need to be considered when protecting workers’ hands with cut-resistance, impact-resistance, or back-of-hand protection at the forefront. While hand injuries are some of the most common injuries among jobsites, they are also some of the most preventable.
Making the Cut
Any type of cut is unpleasant, but the repercussions from a cut to the hand for a worker can be worse than the injury itself. According to the Bureau of Labor Statistics, a single hand injury results in six days away from work on average. For many, this translates to lost wages and diminished abilities upon returning to work. Luckily, within the world of personal protective equipment (PPE), cut-resistant gloves are available to protect workers’ hands from cuts when working with sharp tools and materials.
The American National Standards Institute (ANSI) categorizes cut resistance into nine different levels of protection; the higher the cut level, the more protection the glove provides. To ensure adequate protection, a user must choose the right glove based on the application they wish to complete. Some examples of types of applications for each cut level are listed below:
ANSI A1 (Light Cut Hazards): Light material handling, general work, small parts assembly, forestry, and construction.
ANSI A2-A3 (Light/Medium Cut Hazards): Demolition, material handling, general work, small parts assembly, forestry, construction, wire stripping, pipe threading, cutting and automotive.
ANSI A4 (Medium Cut Hazards): Manufacturing, light glass handling, drywall, electrical, carpet installation, HVAC, automotive assembly, and metal handling.
ANSI A5 (Medium/Heavy Cut Hazards): Metal handling, abrasive/sharp material handling, pipe threading, cutting, drywall, electrical, glass handling and duct work.
ANSI A6-A9 (High Cut Hazards): Heavy metal handling, automotive assembly, sharp metal handling and recycling.
As jobsite safety is emphasized throughout the world, users increasingly need hand protection that is comfortable yet durable. To comply with user needs, many manufacturers now offer a wide range of cut-resistant gloves.
Brace for Impact
Fallen building materials, dropped tools and tasks that involve the risk of pinching and crushing are no strangers to a jobsite. Unfortunately, these common hazards are likely to put workers at risk for impact injuries. Like cut injuries, injuries sustained from impact can lead to lost time and wages and are often even more detrimental to a user’s health. Fortunately, impact-resistant gloves incorporate protective features that can shield the hand from unexpected impact.
Up until 2019, there were no official standards or requirements in place regarding the importance of impact-resistance. In March 2019, the International Safety Equipment Association (ISEA) set a new ANSI/ISEA 138 standard. This standard provided new testing methods for impact-resistant gloves and back-of-hand protection, including a new scale testing impact rating for all finger and knuckle impact sites. With the European EN388 standard originally set up as a pass/fail test, this new standard implemented an impact scale from 1 to 3 to provide more consistency for impact resistance. For example, ANSI/ISEA 1 gloves are classified for protection from lighter weight forces, and ANSI/ISEA 3 gloves are classified for protection from heavier forces:
Level 1 (Low Impact): Allowed an average force of Impact ≤ 9kN.
Level 2 (Medium Impact): Allowed an average force of Impact ≤ 6.5kN.
Level 3 (High Impact): Allowed an average force of Impact ≤4kN.
What Does This Mean for the Industry?
With these safety standards in place, contractors and safety managers not only need to integrate hand protection into their jobsite safety plans, but they will also need to align with OSHA requirements and select the proper solution based on the job at hand. These standards will ultimately help users stay safe and productive while minimizing hand injuries.
Hand protection should not only improve safety but also overall productivity on the jobsite. With these new standards in place, manufacturers, safety managers and contractors have an excellent opportunity to start working towards a jobsite united in hand injury prevention.
For more information or assistance with your Environmental and Health & Safety regulatory compliance needs, contact Ralph Carito at Total Environmental & Safety, LLC (Total) at rcarito@TotalEnviron.com or 908-442-8599.
Thank you for your continued support. If you like what you read in Total’s Monthly EHS Newsletter, please tell your friends and colleagues.
We always appreciate hearing from you, so if you have a suggestion, comment or gripe, please drop us a line at: contact@TotalEnviron.com or call us at 908-442-8599.
Total Environmental & Safety’s (Total’s) most recent blog. Let us know if you enjoyed it.
Page load link